Research example for controlling rust inside steel drum
[Korea] Hong Kong Ting, Manager of INSUNG
1 Introduction
Steel drums are packaging containers that hold and protect internal products. Therefore, the internal surface of the steel drum must be kept clean, ie no oil and any other contaminants. The rust inside the steel drum is an oxide of iron, which can contaminate the interior products. In the past, INSUNG has tried to control the rust in the barrel by the following methods:
experiment method:
1) Dry the weld by blowing dry air after welding.
2) Spray oil mist on the inner wall of the barrel to prevent rust.
3) Spray oil mist onto the weld area.
4) Change the traditional materials using nickel-plated cold coiled sheets.
Among these methods, the use of nickel-plated cold coils works best, so only this method has been used until now. The nickel-plated cold coil is coated with a thin layer of nickel particles on the surface of the cold coil, which is rusted 2.5 to 3 times faster than ordinary steel sheets. Nevertheless, since the high temperature region generated by the welded edge melts the nickel layer, rust is caused from the surface. So a new method is to let air and moisture enter the inside of the barrel to prevent oxidation of the inner wall. This method uses dry air to replace the humid air in the barrel, so that the humidity in the barrel is reduced, and the humid air in the barrel is also reduced.
2. The principle of steel barrel rust
Usually, the corrosion of most metals is related to moisture and oxygen in the air. The reaction between them causes a metal oxide to form on the metal surface, which causes the metal surface to lose its luster. This process is rusting.
The main component of rust is the hydrous oxide Fe2O3nH2O. This is the result of the reaction of the iron surface with water and oxygen. When iron is oxidized at high temperatures, a black hard scale surface is formed which is another type of rust.
The chemical reaction between iron and water and oxygen produces oxides. The reaction equation is as follows:
Fe + 2H2O → Fe(OH)2 + H2
2Fe(OH)2 + 1/2O2 + H2O → 2Fe(OH)3
2Fe(OH)3 → Fe2O3 3H2O
3. Method of preventing rust in the barrel
To prevent the inner surface of the drum from rusting, it is necessary to prevent the inner wall of the barrel from coming into contact with moisture and oxygen.
The following methods can be used to prevent the inner surface of the steel drum from rusting:
1Select anti-rust oil and quantity
The use of anti-rust oil will have an impact on the quality of the coating on the surface of the steel drum. If the anti-rust oil is used too much, it will cause pollution inside the barrel.
2 reduce the surface roughness of the steel barrel
Reducing the surface roughness of the steel drum affects the paint adhesion on the surface of the steel drum, so reducing the surface roughness of the steel drum is not the preferred method.
3 treatment of the interior of the steel drum with zinc phosphate
The chemical treatment of the inner surface of the steel drum with zinc phosphate will pollute the surrounding environment and produce industrial waste water. Therefore, this method is not allowed in Korea.
4 steel drums with internal coating
The internal coating method of the steel drum increases the production cost and may cause the internal paint to react with the contents.
5 Avoid contact between steel drums and substances that cause corrosion of steel drums, such as chlorine and sulfur.
The steel drum production line should be built in an environment where there is no corrosion that can easily cause steel drums, such as away from chlorine and sulfuric acid.
6 Limit the humidity of the air inside the bucket
Studies have shown that reducing the humidity of the air inside the barrel is the best way to reduce rust.
4. Method for reducing the internal humidity of the steel drum
In general, to reduce the humidity in the barrel, the temperature and humidity of the air in the barrel must be reduced before the screw cap is screwed. Before this, we must condense the moisture through careful work.
1) Condensing moisture
Change the amount of water vapor in the air. When the air temperature is low, the pressure changes, and when the amount of water vapor reaches the minimum, it will condense into liquid water.
Taking the closed barrel as an example, when the ambient temperature is lowered, the water is condensed, and the water vapor condenses into water in the barrel to rust the inner wall of the barrel. In order to prevent the formation of water droplets in the barrel, there are two methods that can be used. One is to adjust the temperature of the outside to cause a temperature difference between the inside and outside of the barrel to generate water droplets. Another method is to replace the humid air in the bucket with dry air or nitrogen or argon to reduce the formation of water droplets.
2) Effect of internal temperature of steel drum on rust
Generally, when the air temperature is high, its humidity will be higher. If the air temperature is lowered, the humidity in the air will decrease, and the water will condense out to become liquid droplets.
After the outer surface of the steel drum is painted and dried, the temperature can be as high as 120 ° C. Therefore, it must be cooled for a long time to make the temperature inside the barrel the same as the external environment.
If the temperature of the air in the barrel is close to the ambient temperature in the same area, the moisture in the barrel will decrease. Using this method (blocking the steel drum and letting it gradually cool down to match the ambient temperature) can make the barrel rust later. Moreover, it must be stored until the steel drum becomes cold, and it is preferable to use a cooling device to lower the temperature of the surface of the coated steel drum.
3) Influence of moisture on the inner surface of the steel drum
Under normal circumstances, in Korea, the maximum temperature and the minimum temperature in a day do not exceed 15 °C.
Assume that the volume of the steel drum is 200 liters, the inside is atmospheric pressure, the temperature inside the barrel is 30 ° C, and the relative humidity is 90%. When the temperature is lowered by 15 ° C, the amount of condensable water can be calculated by the following method.
In Table 1, the saturated water vapor is 30.3 g/at 30 ° C, and the amount of water vapor in the barrel is:
{30.3g/ × 0.2 × 0.90 (relative humidity) = 5.454g}
At 15 ° C, the saturated water vapor is 12.8 g / and the amount of water vapor in the barrel is:
{12.8g/ × 0.2 × 1.00 = 2.56g}
Therefore, the amount of moisture condensed is:
5.454g - 2.56g = 2.894g
That is to say, when the temperature in the barrel was changed from 30 ° C to 15 ° C, 2.894 g of saturated water vapor in the barrel condensed and stayed on the inner surface of the barrel. Therefore, to prevent rust in the barrel, 2.894g of water vapor must be condensed into liquid water and discharged out of the barrel.
Table 1. Number of saturated water vapor (relative humidity: 100%, unit : g/)
temperature
Saturated water vapor
temperature
Saturated water vapor
temperature
Saturated water vapor
45 ° C
65.350
31 ° C
32.039
17°C
14.475
44°C
62.259
30 ° C
30.358
16 ° C
13.629
43°C
59.293
29 ° C
38.756
15 ° C
12.827
42 ° C
56.448
28 ° C
27.221
14 ° C
12.065
41 ° C
53.718
27°C
25.760
13 ° C
11.343
40 ° C
51.102
26°C
24.366
12 ° C
10.659
39 ° C
48.595
25°C
23.038
11 ° C
10.011
38 ° C
46.193
24 ° C
21.773
10 ° C
9.397
37 ° C
43.893
23 ° C
20.568
9°C
8.817
36 ° C
41.691
22 ° C
19.421
8°C
8.268
35°C
39.583
21 ° C
18.329
7°C
7.749
34°C
37.568
20 ° C
17.291
6°C
7.258
33 ° C
35.641
19 ° C
15.562
5 ° C
6.795
32 ° C
33.799
18 ° C
15.366
4 ° C
6.358
4) Urban climate conditions in Ulsan, South Korea
Table 2 and Figure 1 below show the urban climatic conditions (including temperature, humidity, cleanliness, etc.) in Ulsan, South Korea for ten years.
Table 2. Weather conditions in Ulsan, South Korea in the past ten years.
January
February
March
April
May
June
July
August
September
October
November
December
Minimum temperature. (°C)
-2.7
-1.3
2.6
7.7
12.3
17.1
21.7
22.3
17.4
11.0
4.8
-0.7
Maximum temperature. (°C)
7.0
8.5
12.7
18.7
23.2
25.7
28.9
29.8
25.8
21.6
15.5
9.9
Average temperature. (°C)
1.6
3.2
7.4
13.1
17.6
21.1
25.0
25.7
21.2
15.9
9.6
4.0
Average humidity (°C)
54.7
56.0
61.6
64.6
68.2
76.6
80.5
79.7
77.2
70.0
64.0
56.8
Average cleanliness (°C)
-9
-7.2
-2.1
4.4
10.2
15.7
21.0
21.2
16.2
9.1
1.6
-6.3
Maximum temperature difference (°C)
9.7
9.8
10.1
11
10.9
8.6
7.2
12.4
14.8
16.8
16.2
7.2
Figure 1. Climate situation in Ulsan, South Korea in the past ten years
According to this information, in the weather in Ulsan, we can see that the average humidity and average cleanliness are higher in the month with higher average temperature. Especially in summer (July and August), the average cleanliness is similar to the lowest temperature, when the barrel is most likely to rust.
That is to say, containers such as steel drums are more likely to rust in an environment with high temperature and humidity in summer.
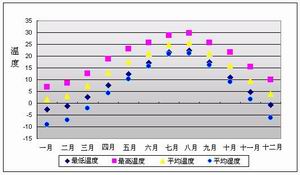
5) Fill the steel drum with dry air to reduce moisture
(1) Production of dry air
In the production workshop of Yingshan Company in Ulsan, the production process of filling the dry air in the barrel is as follows:
Compressor→Gas tank→Filter→Air desiccant→Line filter→Gas tank→Dry air absorber→Filter
First, the air is compressed by the compressor. Second, compressed air enters the gas storage tank. Third, dust and contaminants in the compressed air are filtered through the filter. Fourth, the moisture in the compressed air is liquefied by a lyophilizer. Fifth, the moisture in the compressed air is separated by a linear filter and the contaminants are filtered again and then into the gas storage tank. Sixth, the moisture and contaminants in the compressed air are once again absorbed by the absorbent. Seventh, clean compressed air enters the steel drum through the filter.
(2) Experimental results of sending dry air into the barrel
The result of the experiment of sending dry air into the barrel was the creation of a "dry air production line" at INSUNG in Ulsan. Referring to Table 3 and Figure 2, the dry air index sent to the steel drum is: temperature 32 ° C, pressure 5 kgf / cm 2 , input nozzle diameter 11 mm.
Table 3. Experimental results of feeding dry air into the barrel
Sample number
Dry air before feeding
After the dry air is fed
200 liters
After the dry air is fed
400 liters
Air temperature
temperature
(°C)
humidity
(%)
Cleanliness
(°C)
temperature
(°C)
humidity
(%)
Cleanliness
(°C)
temperature
(°C)
humidity
(%)
Cleanliness
(°C)
maximum
(°C)
Minimum
(°C)
1
36.6
53.5
24.8
36.2
31.7
16.8
35.6
12.6
2.4
30.7
22.6
2
34.5
59.2
25.4
33
32.6
13.4
32.8
13.3
1.1
25.7
23.5
3
34.1
50.5
22.4
33
25.5
9.5
31.6
10.2
3.5
24.1
21.1
4
31.1
51.4
20
29.7
29.2
8.8
28
15
-1
24.6
14.9
5
30.9
61.4
22.6
29.5
29.5
8.9
29.2
12.3
-2.2
23.5
19.8
6
28
47.3
15.5
27.8
25
6.1
27.7
14.9
-1.2
25.3
12.1
7
twenty four
43
10
23.5
22.7
0.8
23.8
13.7
-6.1
19.9
7.4
8
22.6
56.9
13.6
20.6
35.2
5
21.6
14.9
-5.6
17.2
9.3
9
21.3
43.3
8.3
18.5
33.1
1.1
17.8
13
-10.4
11
3.6
10
19.4
52.5
9.5
19.3
19.9
-3.7
18.6
14.4
-8.2
11.3
2.5
Figure 2. Experimental results of sending dry air into the bucket
Table 3 lists the changes in cleanliness and humidity in the barrel before and after feeding 200 liters and 400 liters of dry air into the barrel. When 400 liters of compressed air was fed into the bucket, the cleanliness in the bucket was reduced by 16 °C compared to the bucket without compressed air.
Figure 2 shows the maximum temperature change in January with a temperature difference of 8 ° C ~ 17 ° C (assuming that the chemical product is filled with steel drums in January with the largest temperature difference). At this time, the steel drum that sent 400 liters of dry air into the barrel was left for one month without rust.
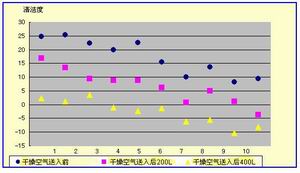
5 Conclusion
The above test is reliable for preventing rust inside the steel drum. Another alternative is to replace the humid air with dry air but the cleanliness is controlled within a reasonable range and is effective for cost savings.
INSHANF's dry air production system at the Ulsan plant has been in use for two years. In the past two years, consumers have never complained that the steel drum is rusting. They said that the steel barrels of INSUNG are satisfactory even in the rainy season.
The Pedal Garbage Bin is designed with strong steel pedal, inner bucket. Some Foot Pedal Rubbish Can are equipped with build-in odour filter placement. You could place odour filters inside the lid to reduce the moisture and odours inside the bucket. It is ingerprint-proof, smudge-resistant Stainless Steel is easy to clean.
pedal dustbin,step trash can,kitchen trash can,pedal bin,garbage bin
TAISHAN YUEXIN INDUSTRIAL GROUP LIMITED , https://www.tsyuexin.com