In fact, the proposal of this program is far from being done overnight. Cerwin worked extensively with other packaging engineers to produce a fairly simple yet impeccable sample that completely changed the main packaging system on the suture market.
The birth of injection trays
There is a real and interesting story about the birth of the Door RELAY suture package around ETHICON. When Cerwin brought the samples to the mold analysts and potential suppliers of injection molded products, people told him that this thing could not be injected because its tolerance requirements were too stringent. Cerwin recalled: “We have found injection molding factories, but they do not want to spend on research and development. They do not believe that ETHICON products can persist.â€
Later, finally a supplier named Unimark Plastics bravely accepted this challenge. Today, nearly 2 billion suture plates are injection molded.
After several generations of development, the trays have evolved from a monolithic design with a semi-automatic winding of sutures to a two-piece design, which can be automatically produced on almost all packaging production lines. The cost per tablet is lower, and the performance of the tray is also obtained. strengthen.
With more than 200 companies and approximately 100,000 employees worldwide, Johnson & Johnson is one of the most famous brands in the field of health products. The company's products range from medicines and health equipment to OTC drugs and personal health products. It has been growing at a rapid rate since its establishment in 1887. In 1887, Johnson & Johnson brought the first sterile wound care product to the healthcare business, including sterile surgical bandages and bactericidal threads that can be absorbed by the body.
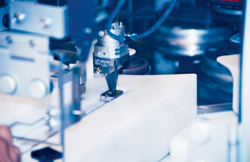
A hinged robot picks up the needle from the shuttle holder and places it on the plate.
ETHICON's Exploration
The manager in charge of ETHICON product packaging development said: “The performance of Johnson & Johnson is based on disinfection capabilities. We are the first to take the lead in all kinds of disinfection methods. The first is steam sterilization, and finally chemical products such as ETO ( Ethylene oxide) followed by cobalt 60 (gamma rays)."
In 1949, ETHICON was formally established as a division of Johnson & Johnson in Somerville, New Jersey, and began to add various production lines to meet the demand growth and new challenges brought about by the professional development of operating theatres. The company’s range of sutures has also been expanded. In addition to the addition of natural fibers, silk, cotton, and flax to the gut, the company has developed synthetic fibers that can absorb and cannot be absorbed, as well as stainless steel and tantalum.
Since the early 1990s, ETHICON Products has established several complementary companies specializing in the production of wound care, gynecological supplies and cardiovascular surgical equipment. ETHICON Global Products Corporation operates independently from these divisions. ETHICON operates 10 independent manufacturing companies and several distribution companies worldwide, with more than 4,000 products. The company's suture series products have everything. At present, the company's products account for more than 70% of all sutures sold worldwide. In the United States, ETHICON's total market share is approximately 80%.
One of the areas explored by ETHICON product companies is to change the existing suture package. The sewn package consists of a paper folding machine secured in a foil pack and a peelable pouch made of DuPont HDPE/PE/Flake. Since the end of 1800, the company's products have been continuously evolving. The first product was a small glass tube fixed in a canister filled with disinfectant. The paper tray is a huge improvement over the previous technology, but ETHICON The engineers and technicians of the product companies see that there are still opportunities for development in user-friendliness.
The realization of the idea
With the help of ETHICON Products' mechanical plant, Bob Cerwin used polyvinyl chloride to create a two-piece disc real model and used a little foam to hold the small needles. One of the advantages of this new design is that it can position the needles securely, ensuring that the needles are in the same position in each package. This is of great benefit to the surgical environment because the danger of spreading AIDS, STDs and other blood viruses through needles is now very serious. In addition, this design fundamentally eliminates the chance of the needle puncturing the outer packaging of the sheet and impairing the sterility of the product. This new design also provides greater “stitched memory,†which means that it can reduce the number of steps and allows the sutures to be unrolled directly from the disc, which was previously manually wound onto the origami. Injection trays are cheaper than paper trays and can be reused, which is good news for environmental protection.
Although the customer's panel discussion and market research showed that the response to the sample tray was very positive, Cerwin recalled that although the management of the ETHICON product company approved the development of the new design, it has reservations because the change is indeed It is too big. It was at this session that the lucky god patronized and Bob Cerwin’s colleagues mentioned that another company tried to challenge ETHICON’s 80% share of the American suture market. Cerwin said: "Suddenly, I obtained this project. This project is no longer merely a solution to the coordination problem, because we face a competitive threat."
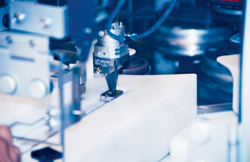
After the tray is full and labeled, it is picked up by the robot and placed in the hopper, and the tray is manually removed from the machine.
ETHICON Products has introduced Door RELAY packaging in 1991 by working closely with Unimark. This thin polypropylene design is less than 3 1/2 inches long and 1 1/4 inches wide. Each tray is made of a single piece of material surrounded by tabs that can be folded off after the stitches are wound. According to the new tray design, the semi-automatic winding of the suture can be achieved, and the suture can be accurately placed into the tray using the vacuum principle, and then the tab can be closed to prevent the suture from coming out.
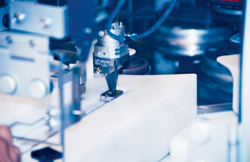
The pallets are stacked on the green box and shipped out of the assembly room and transported to the pouch forming machine.
Door RELAY packaging is just the beginning of the Zipper 1 (Z1), Z2 and Z3 tray series, each with more varieties than the previous generation, taking Unimark's injection molding capabilities to new heights and enhancing ETHICON Product company's packaging automation level. Cerwin said: "We have made breakthroughs and then we have continued to make progress."
Starting from Z2, the monolithic design of the ETHICON product company has become a two-piece, ultrasonic welding on Unimark's production equipment. Due to the use of stylus winding technology, this tray has enabled ETHICON product companies to take a further step towards automation in winding machines. Cerwin said: "We emphasize that when looking at these designs, we must realize that the precision part is part of the automation equipment (stitch coiler) and it will also become part of the package." He said: "Designing paper trays When it comes to equipment, it is almost impossible to think about equipment. But when designing plastic pallets, it cannot be done."
The ETHICON product company's sutures are wound and packaged at many plants around the world. Each factory has a special division of labor to produce specific suture products, such as monofilament or braided sutures that are easily absorbed or not absorbed, and gamma-irradiated ETO sterilization products.
The ETHICON San Lorenzo factory is located on the island of Puerto Rico and it mainly packs non-absorbable sutures. Although most sutures are sterilized by cobalt radiation, PROLENE polypropylene sutures used for cardiovascular, ophthalmic, and neurological surgery are sterilized using ETO.
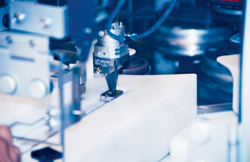
An on-line printer is printing various data on the label, and the label is printed and sent to the Z3 assembly room.
Automatic winding and packaging
During a recent visit to the San Lorenzo plant, PD editors had the opportunity to see various generations of suture winding technology, from paper tray winding to the almost fully automated Z3 packaging process. According to Delfin A. Lorenzo, the plant's technical director, we are now preparing to phase out the trays and replace them with Z3 pallets. The factory's winding operations are somewhat less automated than most Z3 pallet production lines. These are mainly used with the two-armed code to deal with smaller or two stitches with needles. The final conversion from paper to plastic trays would be those needles that are too large to fit in the Z3, such as a 3-inch cord span. Cerwin said that these will be solved with another tray design in the next few years.
At present, these products are still using origami machines and are wound manually by 8-bit winding method. This requires the operator to do many wrist moves. The operator has to rest twice in each shift. â€
After winding, the filled tray is packaged in a pre-printed tear-off foil supplied by Alcan Packaging. The origami machine is heat-sealed into the foil bag manually using a rotary table designed by ETHICON product company. The foil is printed with a variety of information, such as tip size, stitch size, product name, and opening instructions, all of which are pre-printed using a 7-color flexo press from Mark Andy or Perfecseal. The foil bag is then loaded into a peelable heat set bag. The heat setting package uses a bottom web provided by DuPont Tyvek 2FS and is sealed with a top mesh made of Perfecseal's transparent polyolefin film.
The sachets are formed on a Multivac reel machine. There are a total of six such machines of various types. The ETHICON product company uses these machines to seal the film instead of Tyvek (high-density polyethylene synthetic paper), which Cerwin said is to obtain a "consistently good packaging." He said: "Whenever possible, do not use a tear-away foil pouch. The stitches are wound onto origami printed by the southwest company of John Henry Packaging Group and placed in a Tyvek/foil pouch."
In the final step before sterilization, the on-line Bell Mark thermal transfer machine prints the barcode, expiration date, and lot number on the Tyvek/film pouch.
From the complete manual packing operation to the semi-automatic winding operation, the factory has eight workstations where the operator winds the thread to the Door RELAY father's school to render 7 stations for wrapping the Z1 tray. In this process, the operator manually put the needle on the pneumatic winding machine, and the pneumatic winding machine wrapped the thread on the tray and then closed the tab. Then, the tray will get a "cover", which is a pre-printed dieboard label. Labels are attached to the two nodes of the tray. The lid was printed on a Mark Andy press using a cardboard custom made from the Monadnock paper mill.
The secondary packaging for Door RELAY 1 products is a pre-printed peelable small foil pouch (for environmentally sensitive or absorbable sutures) and Tyvek/Film pouch (for non-absorbable products) manufactured by Amcor Corporation. . In order to produce foil packaging trays, ETHICON product companies use filling/sealing equipment custom-made from Harro Hæ liger, and Multivac equipment is used to package non-absorbable products in Tyvek/film.
although
Claw feet are accessories of freestanding cast iron bath tubs. Color of claw feet can be white, black, chrome, brushed nickel and oil rubbed bronze. Material of the feet is cast iron. The claw feet are in many different shapes and sizes.
We supply faucet of Cast Iron Sink.
Tub Faucet,Roman Tub Faucet,Freestanding Tub Faucet,Clawfoot Tub Faucet
Anping Sunshine Sanitary Ware Co., Ltd. , https://www.sunshinebathtubs.com